On the ground, the International Space Station would be an odd
looking building - but space is an odd place to live!
by
Patrick L.Barry
Homes on Earth
provide shelter from the wind and rain. But a home in Earth orbit
must shield its occupants from the solar wind, and it must
withstand a steady rain of dust-sized meteoroids, many moving faster
than a speeding bullet!
A terrestrial
house has insulation
to keep the air inside cool or warm, but a space home must be tightly
sealed just to keep the air inside.
The structure
of earthbound buildings must support a constant gravitational pull
of 1-g. In contrast, an orbiting structure's design should make
sense in microgravity, and at the same time be able to withstand
the tremendous 3-g acceleration of a rocket blasting into space.
For these and
other reasons, building a structure for living in space poses a
different set of design challenges than building homes on the ground.
The first thing
an architect would notice about building in space is the pull of gravity
-- or rather the lack thereof! A freely-falling space home in Earth
orbit can take a wider variety of basic shapes than homes on the planet
below.
"It's in free
fall, so there's no need to say 'this is up' and 'this is down'
from the standpoint of the station's architecture and structural
integrity," said Kornel Nagy, structural and mechanical systems
manager for the International Space Station (ISS) at NASA's Johnson
Space Centre.
For example,
science fiction writers often imagine that a space station would
be wheel shaped. As seen in the Stanley Kubrick / Arthur C. Clarke
science fiction classic 2001: A Space Odyssey, these ring-shaped
outposts would slowly rotate to create a centrifugal pull that acted
as a false gravity. Other visionaries, such as NASA's own Wernher
von Braun (see our article, Wheels
in the Sky), also saw a spinning wheel as the most likely space
station design.
So why does
the ISS look more like an Erector Set than a big hamster wheel?
"Even though
(the wheel design is) an elegant concept," says Nagy, "you have
to think in terms of the current launch vehicles that we have and
how you get all the pieces on board and assembled into a unified
body."
"So the option
that was looked at is to take the pressurised compartments up in
segments that are as big as you can lift in a particular launch
vehicle," he continued. "In our case, it's the Shuttle payload bay."
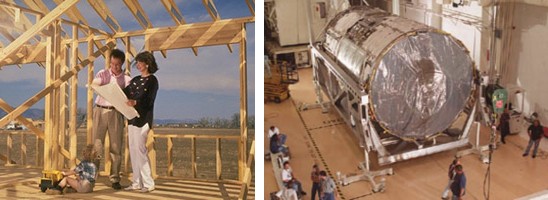
NASA
Building
a home for living in space requires a little more than plywood
and two-by-fours. Titanium, Kevlar, and high-grade steel are
common materials in the ISS. Engineers had to use these materials
to make the structure lightweight yet strong and puncture-resistant.
|
Because each
of the aluminum-can shaped components of the Station has to be lifted
into orbit, minimising weight is crucial. Lightweight aluminium,
(rather than constructing a steel
building), comprises most of the outer shell for the modules.
This shell must
also provide protection from impacts by tiny meteoroids and man-made
debris. Because the ISS zips through space at about 27,000 km/h,
even dust-sized grains present a considerable danger. Man-made debris,
a drifting legacy of past space exploration, poses an even greater
threat.
To ensure the
safety of the crew, the Space Station wears a "bullet-proof vest."
Layers of Kevlar, ceramic fabrics, and other advanced materials
form a blanket up to 10 cm thick around each module's aluminium
shell. (Kevlar is the material used in the bullet-proof vests used
by police officers.)
"This protective
shielding was tested by shooting at it with high-velocity guns to
verify that it is indeed a good protection material," Nagy said.
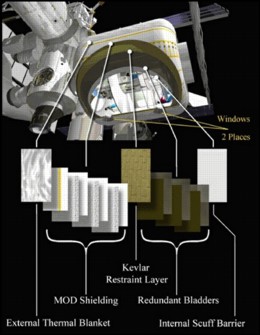
NASA
Layers
of Kevlar and other impact-resistant materials reduce the
chance that small debris could penetrate the modules' walls
and endanger the crew.
|
Designers had
to leave a few holes in this armor so the crew could occasionally
enjoy the spectacular view.
A typical window
for a house on Earth has 2 panes of glass, each about 1/16 inch
thick. In contrast, the ISS windows each have 4 panes of glass ranging
from 1/2 to 1-1/4 inches thick. An exterior aluminium shutter provides
extra protection when the windows are not in use.
The glass in
these windows is subject to strict quality control, because even
minute flaws would increase the chance that a micro-meteoroid could
cause a fracture.
In orbit, a
major force is the pressure of the air inside the ISS, which presses
on each square inch of the modules' interior with almost 15 pounds
of force. (Homes on Earth also have this internal pressure, but
the external pressure of the atmosphere balances it out.)
But even before
reaching orbit these modules must also hold up to the massive stresses
of launch.
"The structure
has to withstand the loading it will see while being transported
to orbit, which is a pretty intense environment," Nagy said.
As the Shuttle
climbs toward the edge of space, every piece of the ISS module inside
will "weigh" three times normal. The structure of the modules must
handle both this loading along the long axis during launch and the
internal air pressure while in orbit.
Once the Shuttle
has carried a module into orbit, the task remains to securely attach
it to the rest of the Station.
The US-designed
Common Berthing Mechanism (or CBM) links together the modules. To
ensure a good seal, the CBM has an automatic latching mechanism
that pulls the two modules together and tightens 16 connecting bolts
with a force of 19,000 pounds each! This huge force is needed to
counteract the tendency of the internal air pressure to push the
modules apart and to ensure a good air-tight seal.
"A lot of development
work, a lot of testing, and a lot of certification went into the
CBM to be able to achieve that reliable seal," Nagy said. "So far
it's worked well."
|